Egypt
Ras Ghareb – Red Sea
Oil & Gas
Stress Analysis
Capital Gas
- Completed
19 November, 2020
25 November, 2020
AL Hamed Pipe line Gas Stress Analysis, Ras Ghareb, Egypt
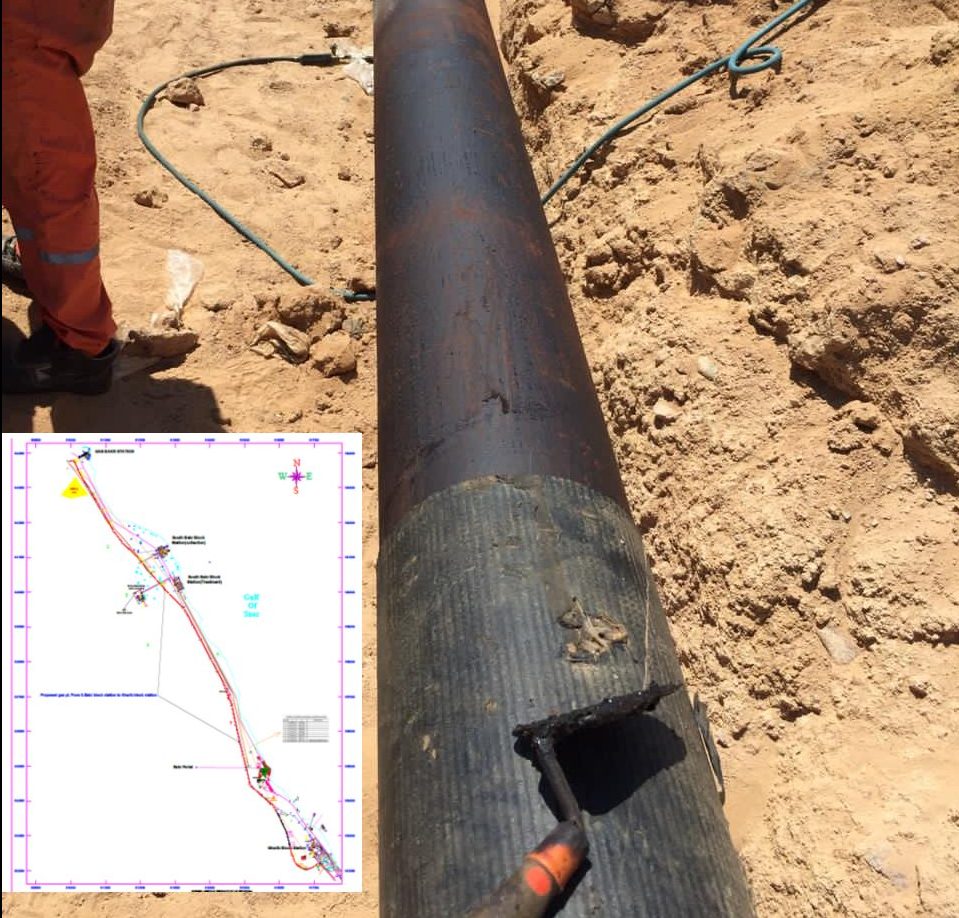
Integrated Engineers team has been involved as sub-consultant and designer in Pump station rehabilitation project
CAPITAL GAS AND PARTNERS signed a contract with EGPC and GPC to build and operate a Gas
Processing station in Ras Ghareb area within the premises of GPC. According to which, the company
was granted a land and a daily supply of 15 MMSCFD of sour gas where both (Company and GPC)
could share benefits from processing the gas.
This sour gas after treatment is giving the following products: butane, propane, condensate, Sulphur
and residue gas. All the butane and some of the propane are combined at storage vessel, the remainder
of the residue gas goes directly to GPC in its same form for , condensate and Sulphur will be stored in
special hangar.
The sour gas will be supplied to the station through 4 fields (Gharib, Fanar, Shukeir 3 and El-Hamed).
All flowlines from the fields to the plant already exist, except El-Hamed which is yet to be installed.
The following shall be covered: – Compressor Head verification
Transient analysis for the following cases:
- Pressure & temperature diagram reporting
Upsurge and downsurge pressures identification
Surge suppression equipment sizing
The steady state and surge analysis scope summarises the results of the following analyses:
- Confirmation that proposed 8” CS pipeline size, consistent with existing project use, is sufficient to satisfy flow demand and ensure MAOP of 1566 psig are not exceeded;
- Identify P/T profile for both summer and winter case;
- Produce phase envelope, evaluate hydrate risk and propose hydrate mitigation measures if any;
- Identify velocity profile along production system with respect to erosional and minimum/maximum velocity constraint;
- Confirmation that the pipeline shall not be subjected to any pressure exceeding MASP during any transient case i.e. line packing while compressor is still running.